Plastic parts
The possibility of accessing 3D printing as a resource enabled us to create our own molds (tooling) to facilitate the production process, as well as to build inputs for the waveguides.
Initially, the plastic parts arose from the need to replace the plastic lids used as lids with 3D printed plastic lids.
Seeing the potential of 3D printing, we designed a prototype of a portachain to hold the antenna cables, as well as molds to facilitate the drilling of the waveguide pipes.
The current portachain allows us to replace procedures such as welding or resining, shortening production times and costs as well. The process to arrive at these designs and the different previous prototypes are recorded here.
This research process involved familiarizing ourselves with the design tools in Freecad and practice with the printer. Currently we are about to access a training course at the UTN (National Technical University) to perfect the prints.
Lids
Our first design allowed us to improve the performance of the antenna, since the plastic strips that we used as a cover interfered with the waveguide signal.
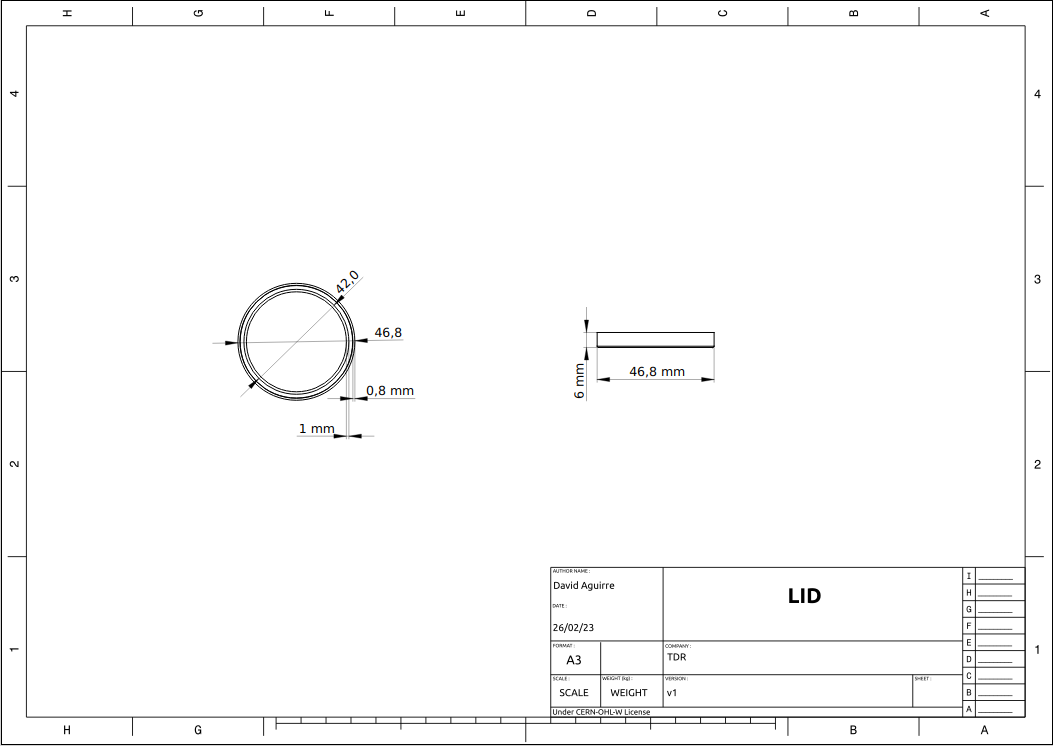
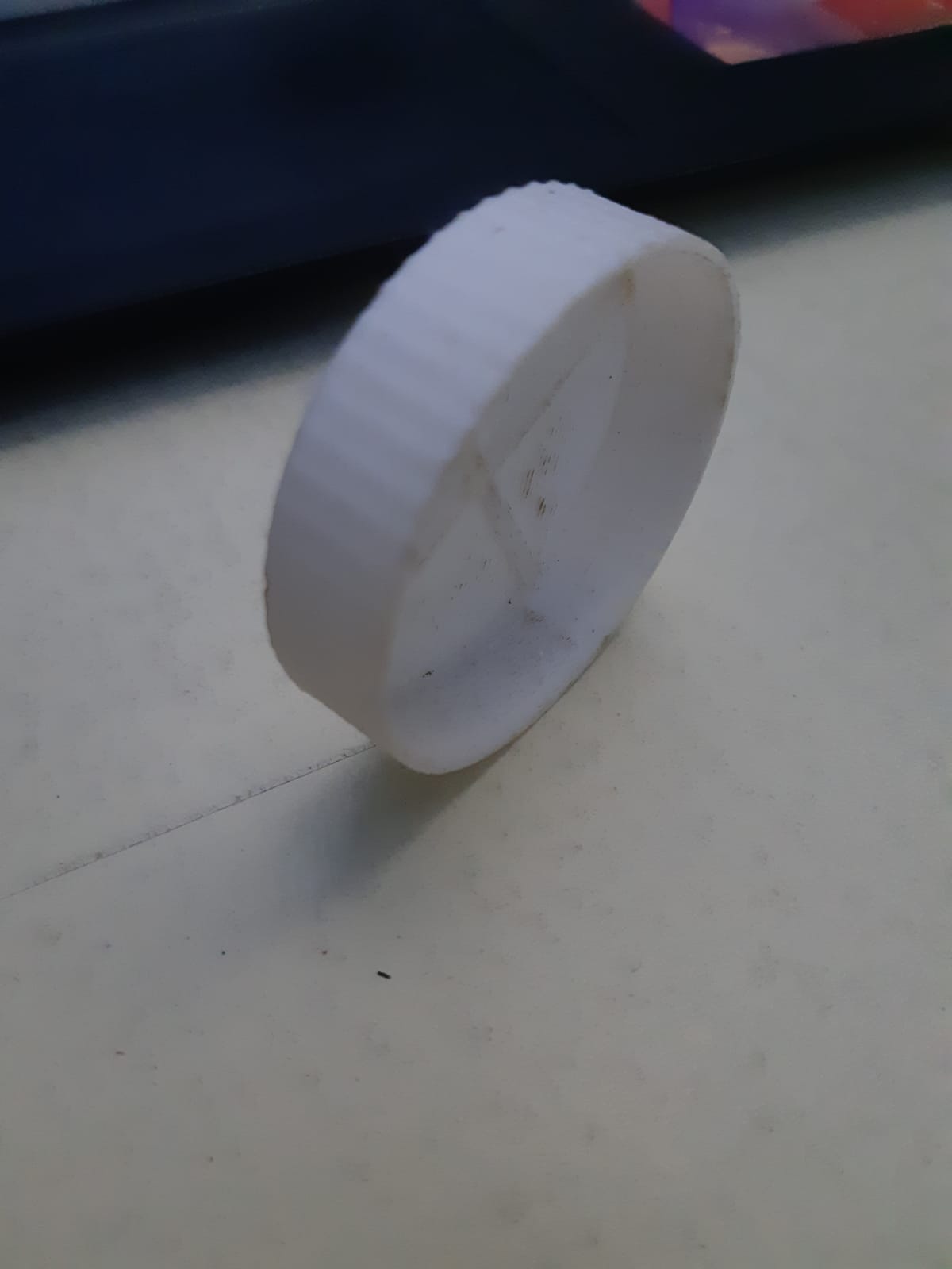
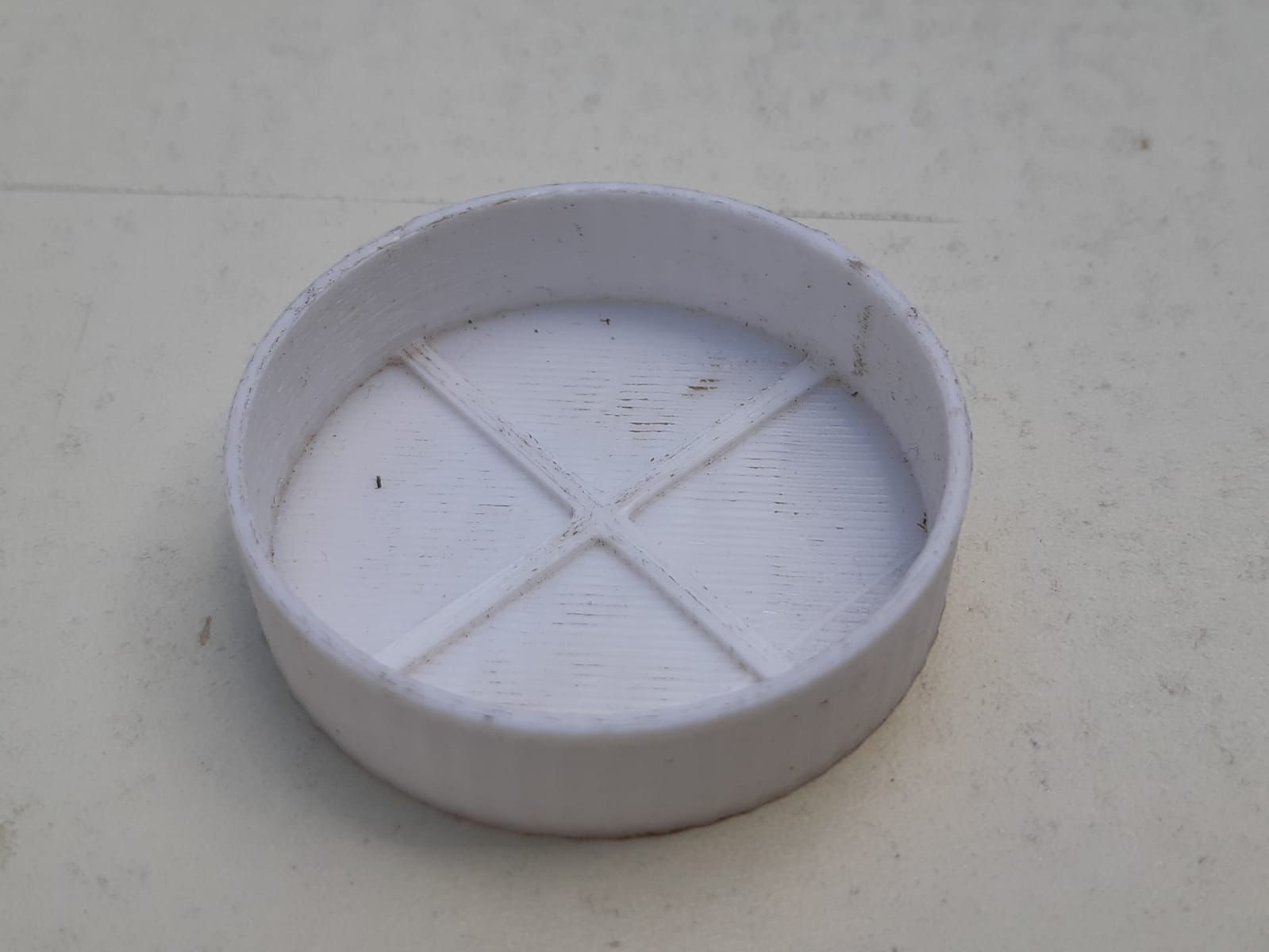
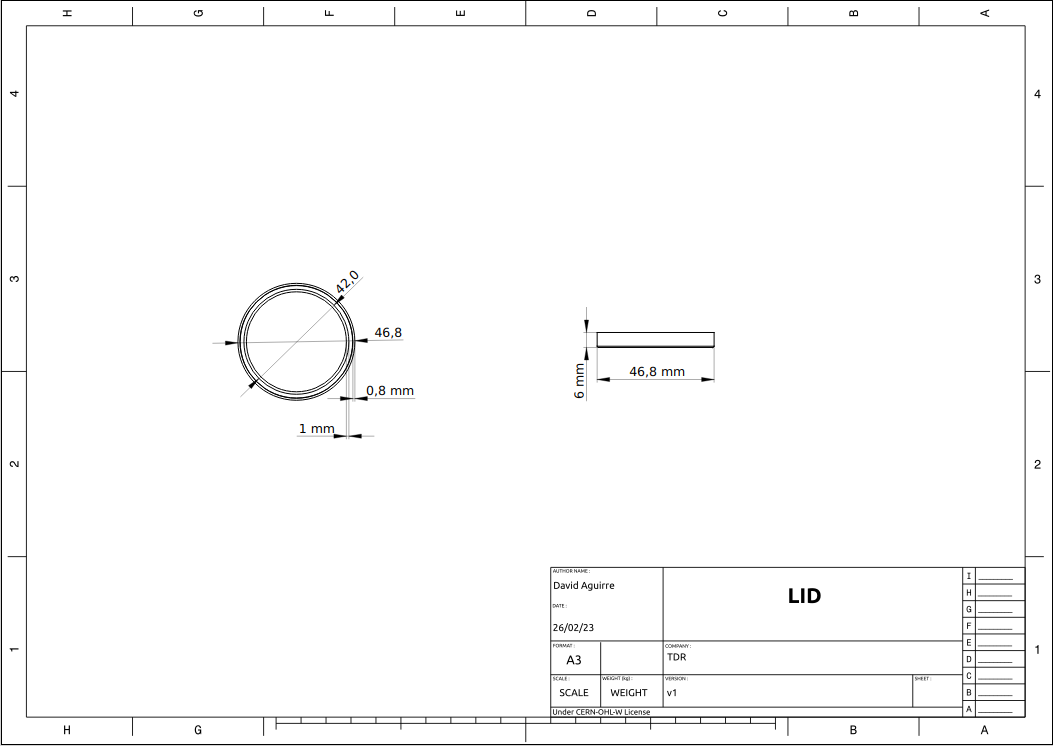
Drilling mold
This design gives us precision when drilling holes in the waveguide, speeding up the production process.
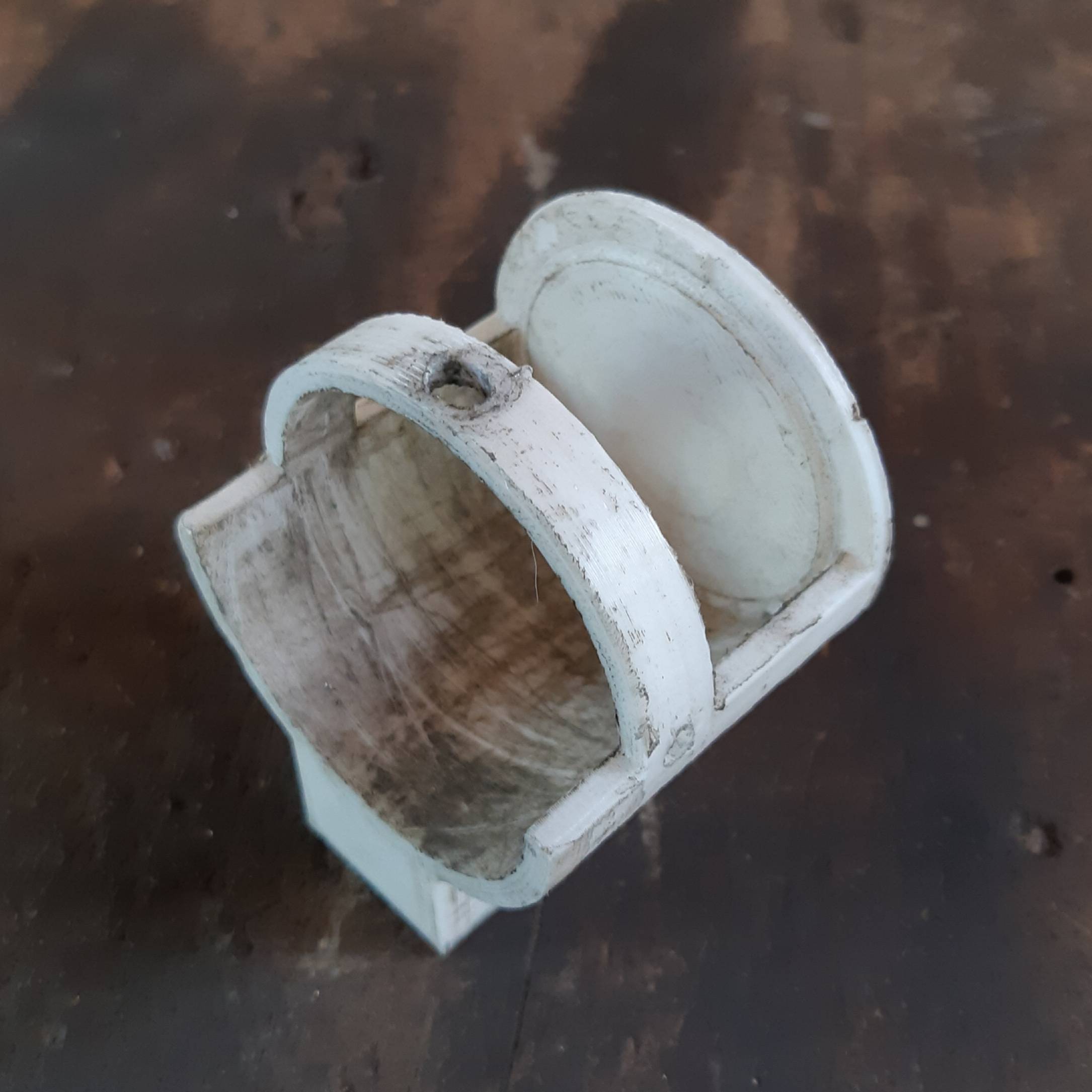
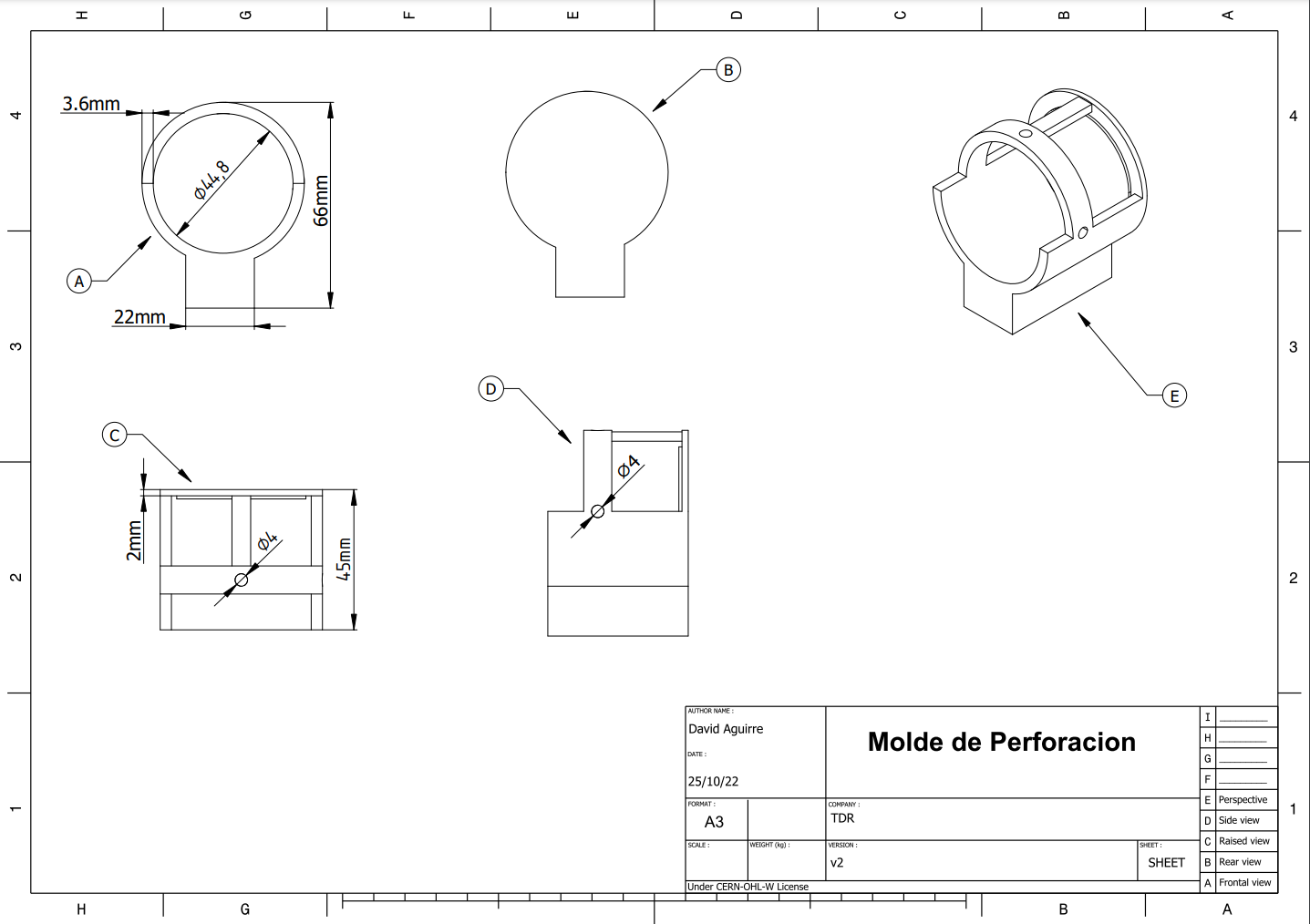
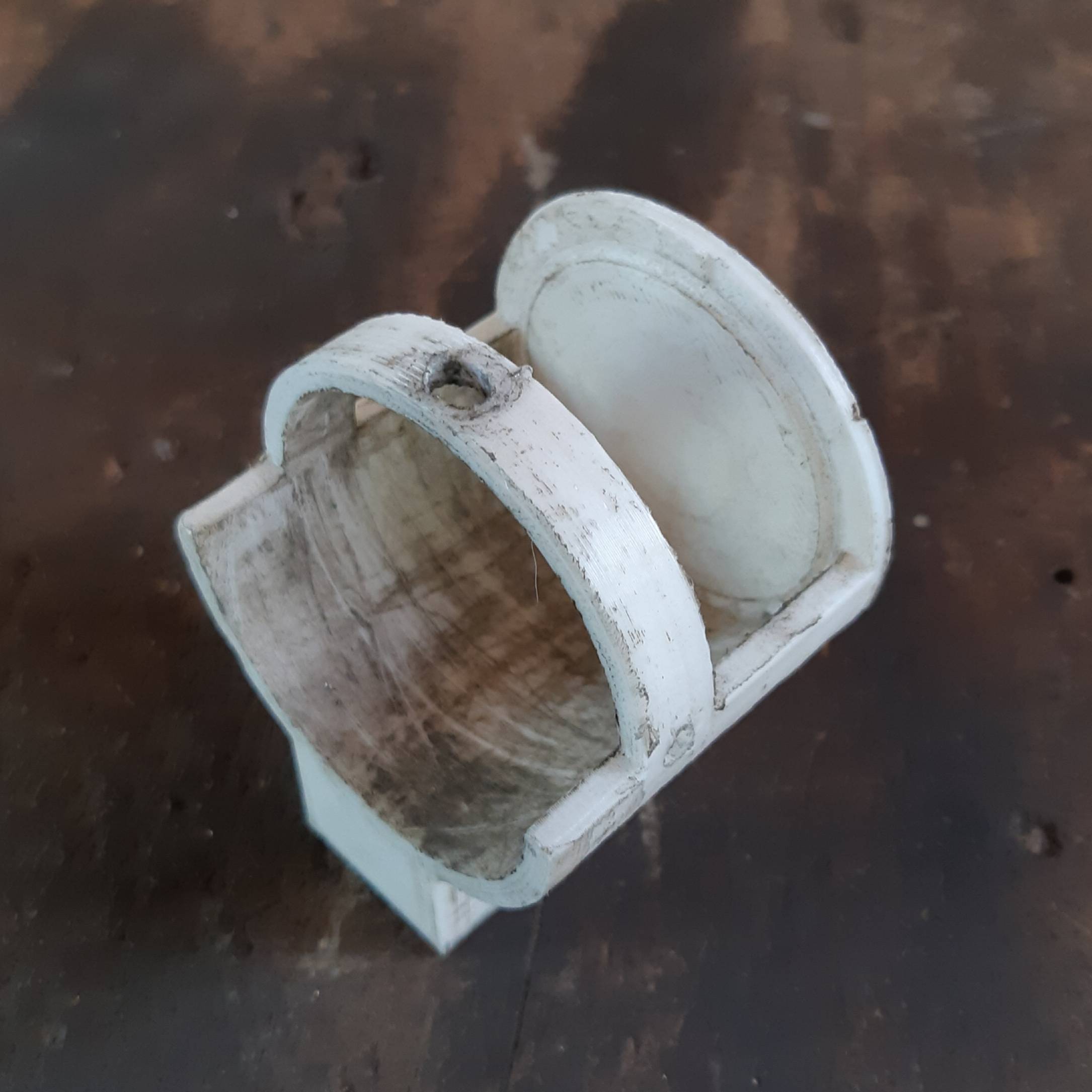
Portachain
The possibility of designing these parts allowed us to optimize the way of fastening the cables, which was a challenge in the previous prototypes, meaning higher cost and production times.
The first design was fragile because the material we used, PLA filament, was not suitable for the antennas, as they are exposed to sun, rain and wind.
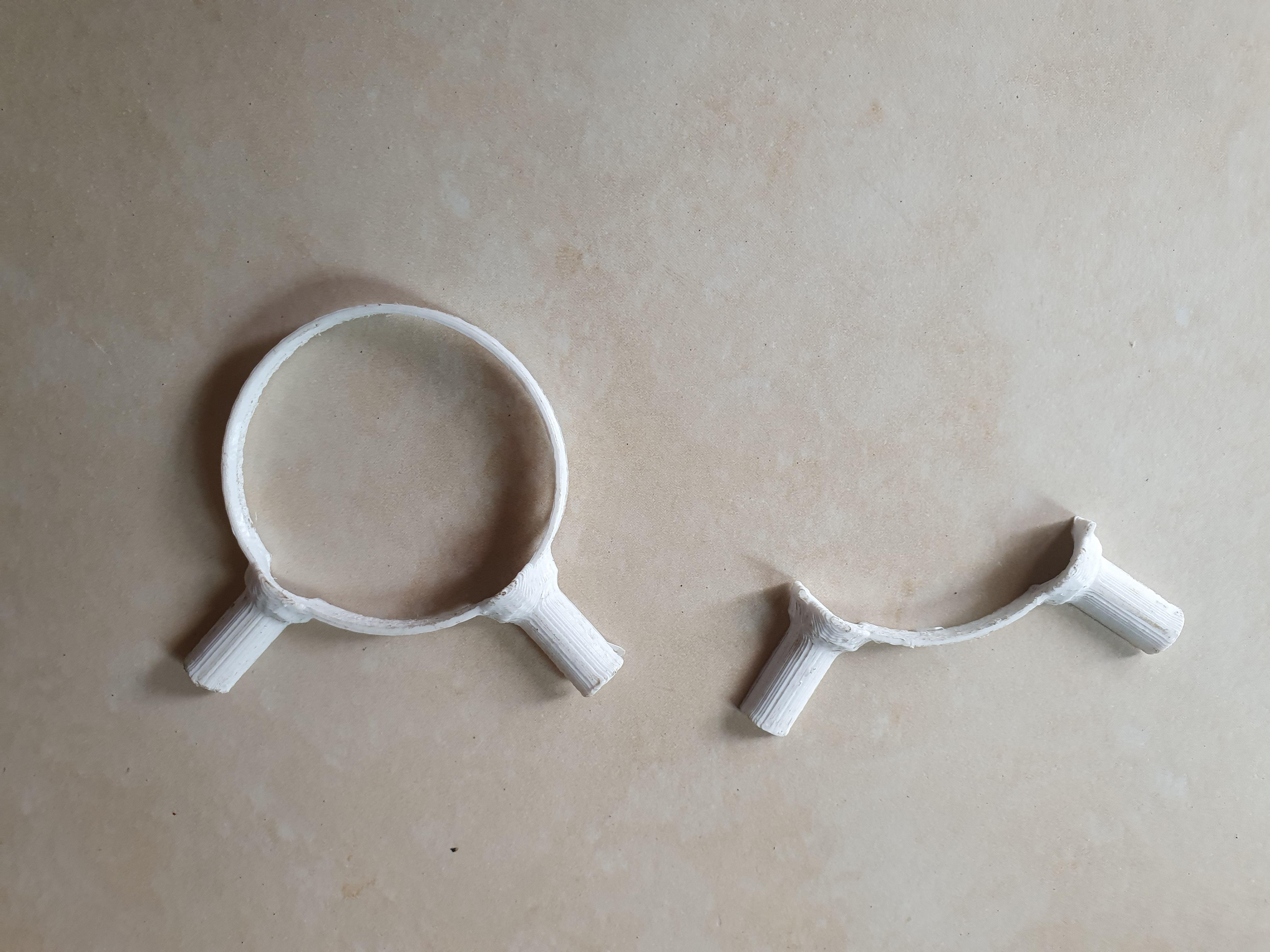
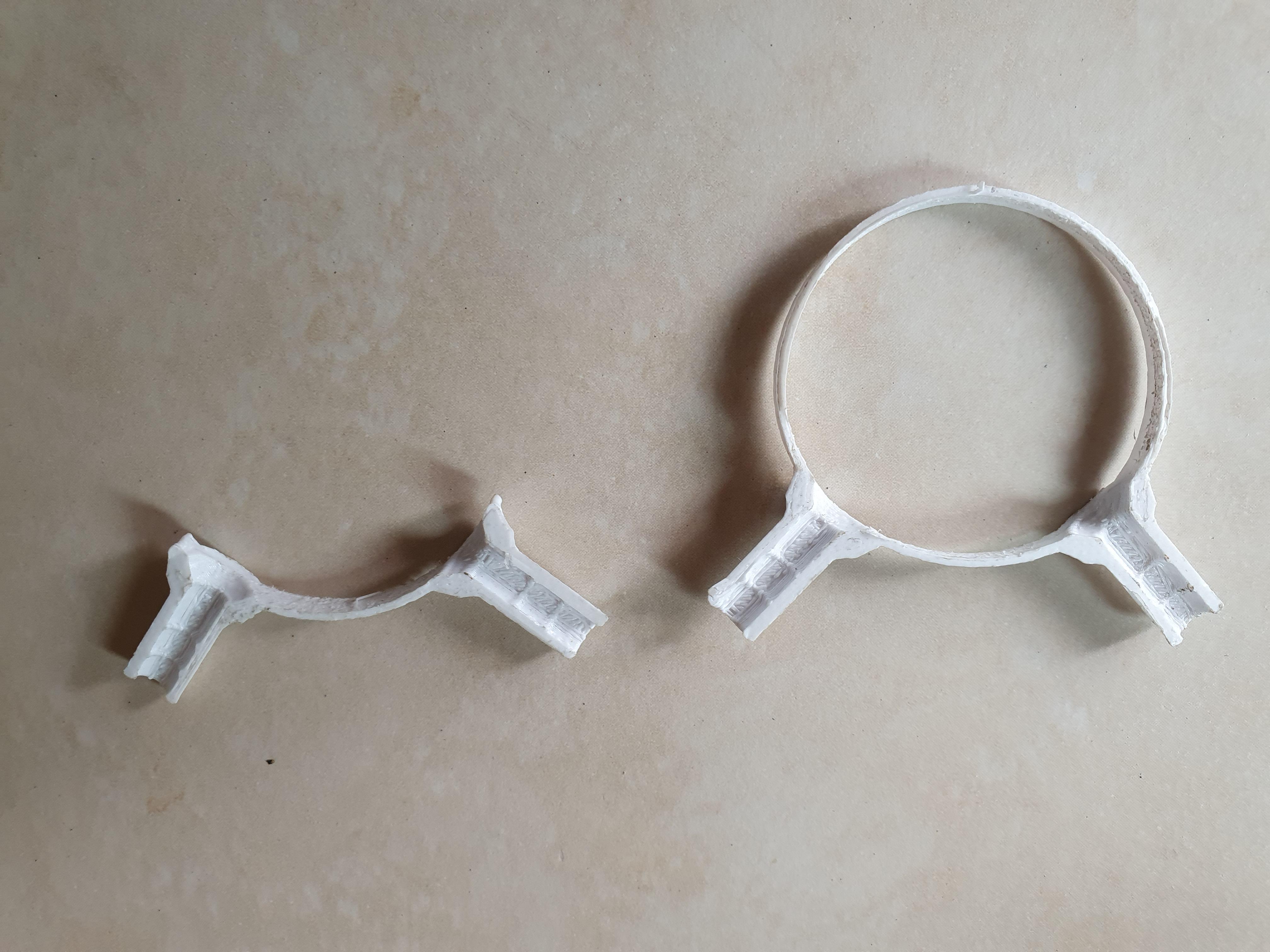
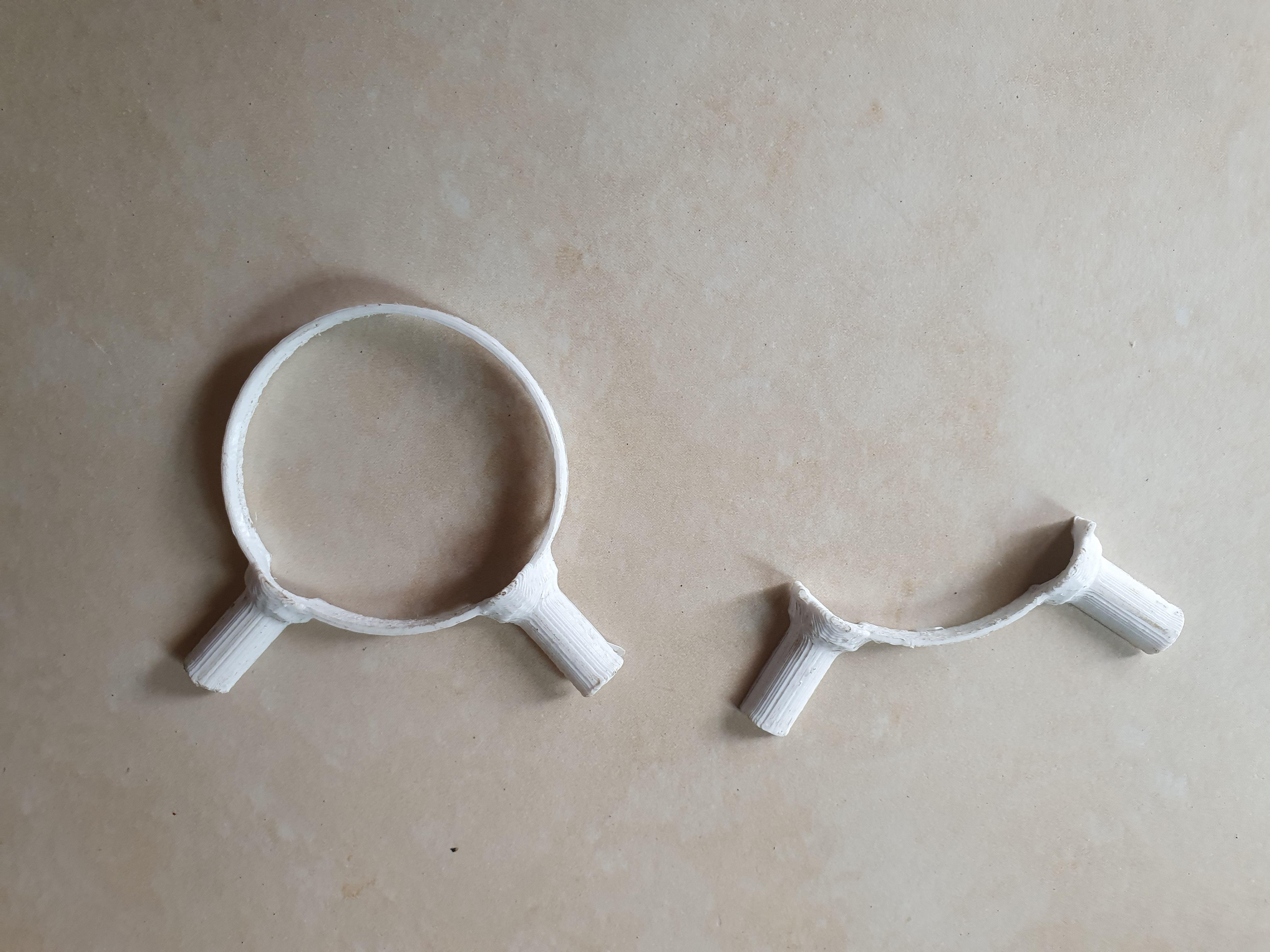
The second version of the portachain was designed taking into account the increased thickness of the part to give it more solvency, and the material, which was replaced by PETG filament.
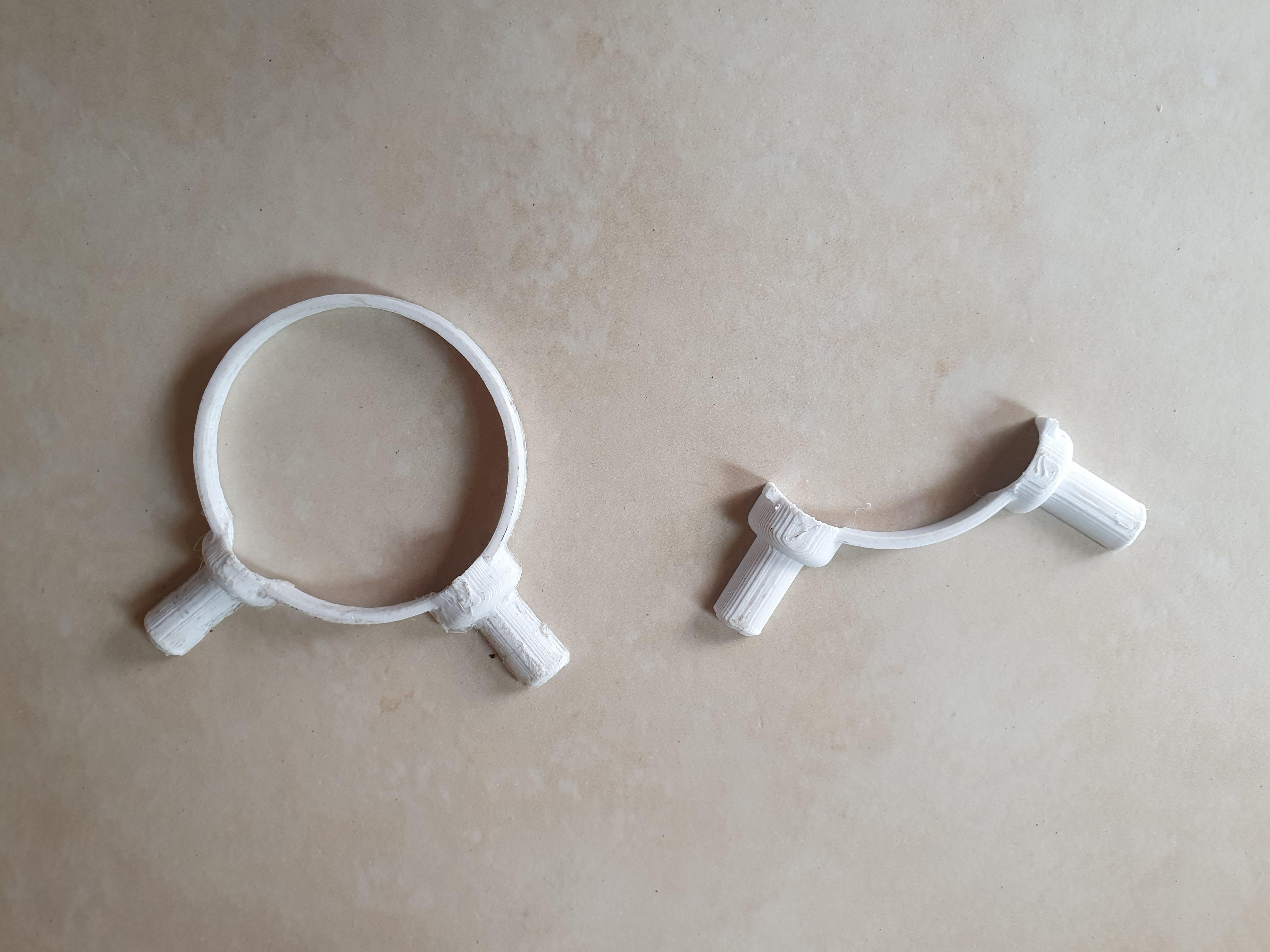
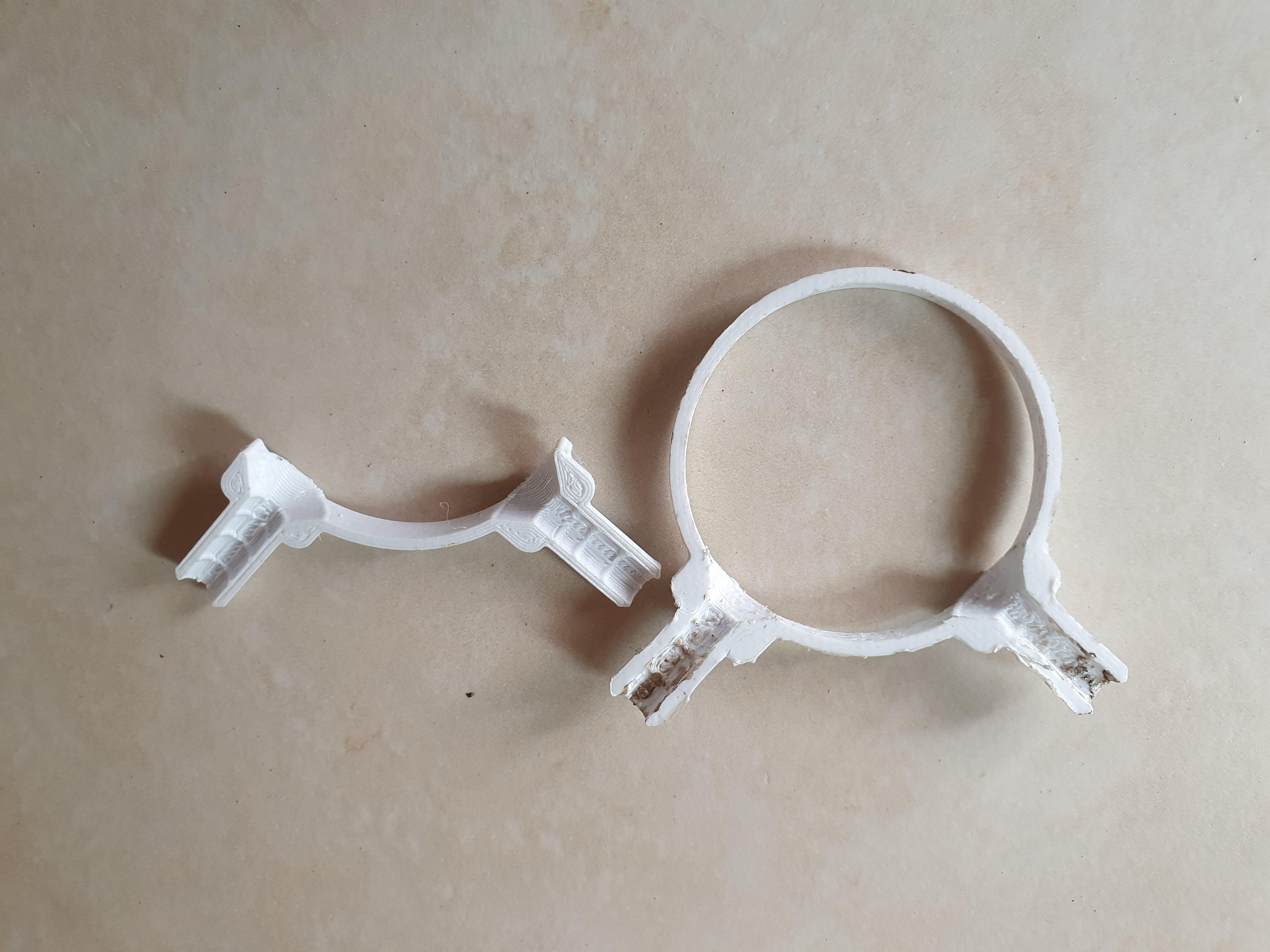
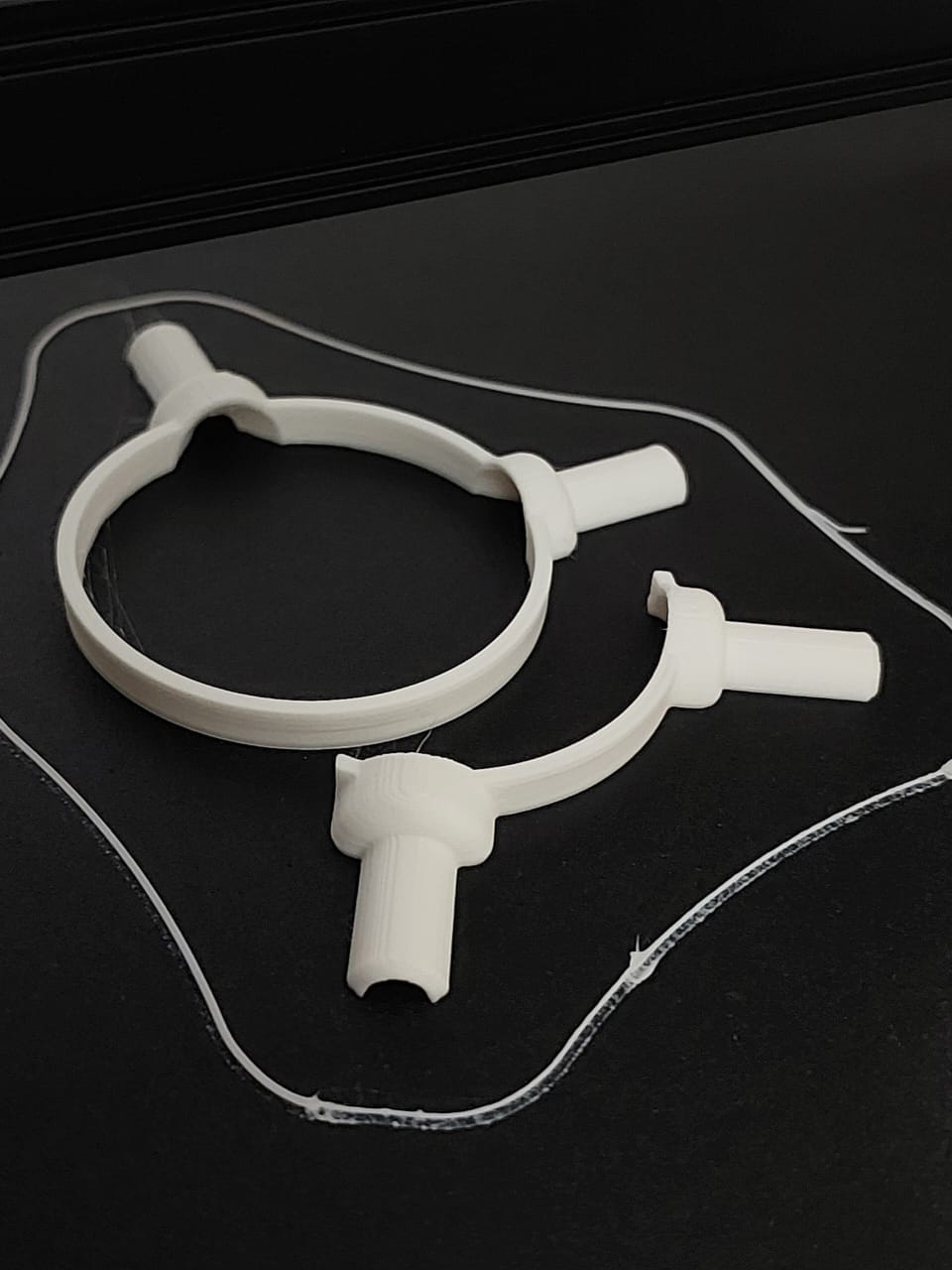
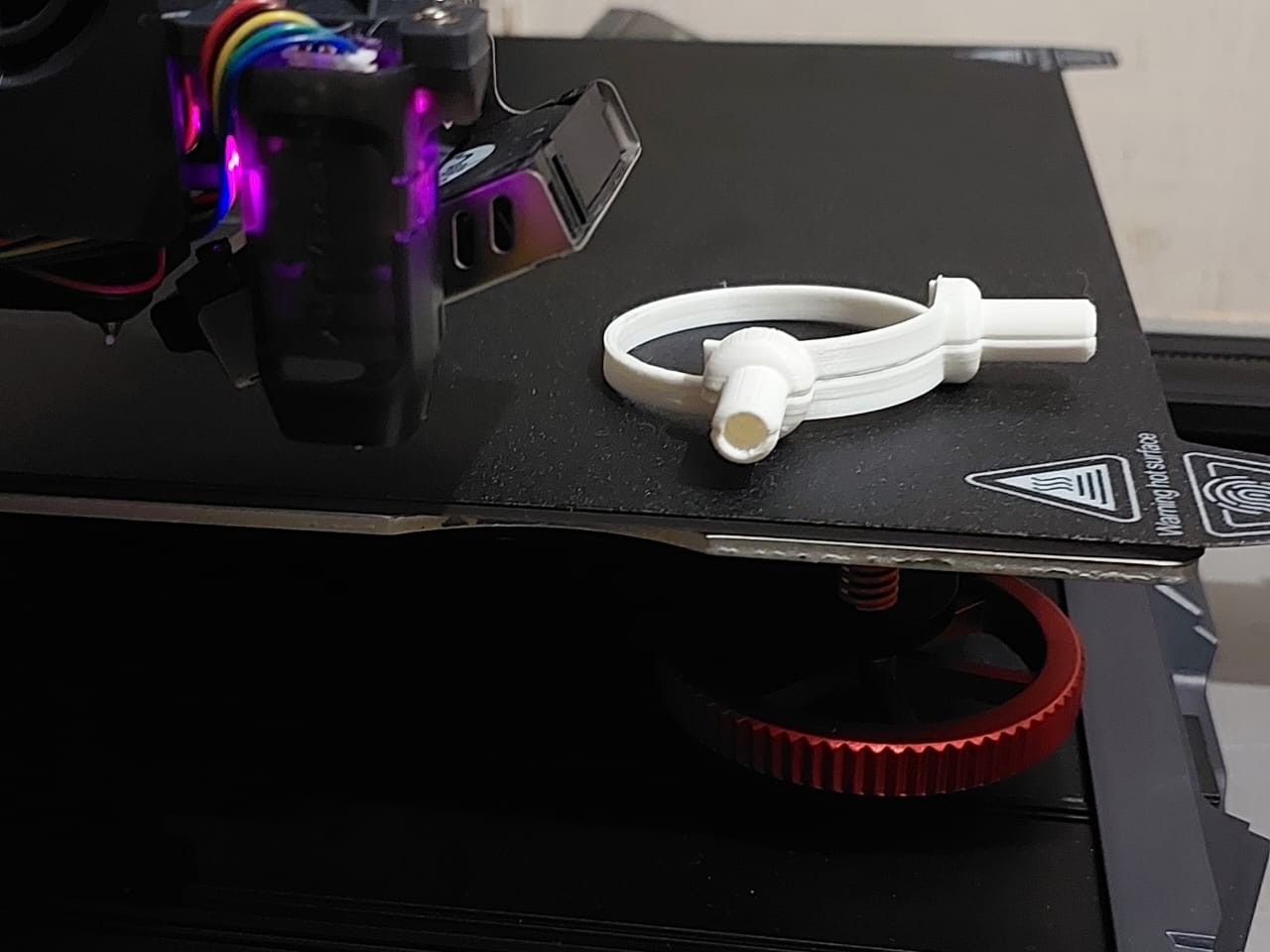
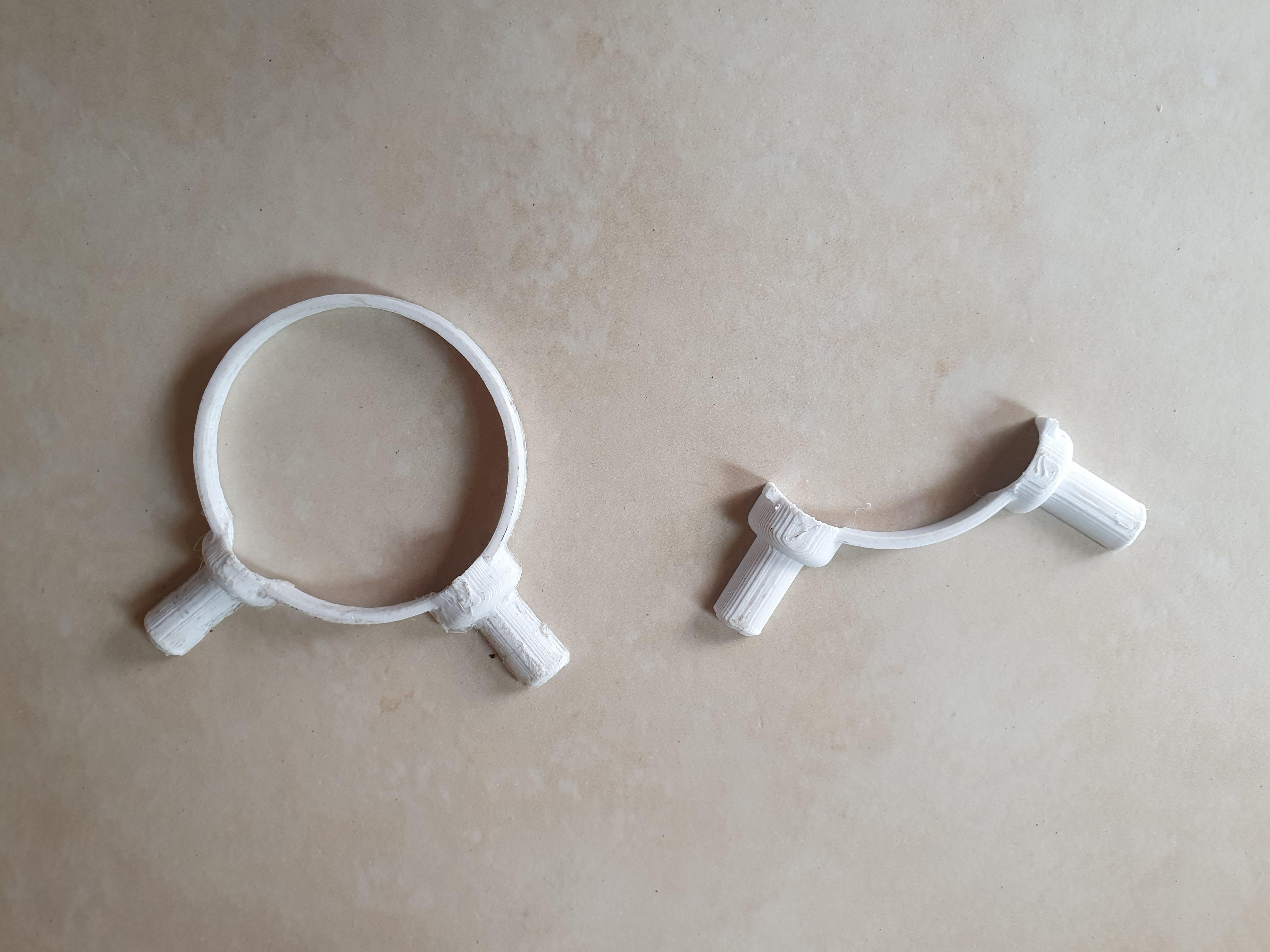
The first designs did not allow us to hold the cables as expected.
Then we realized that in order to give it a better finish and a better grip, we had to attach a 3/8 crimped aluminum pipe ring to the cable holder, thus providing the expected firmness to hold the cables.
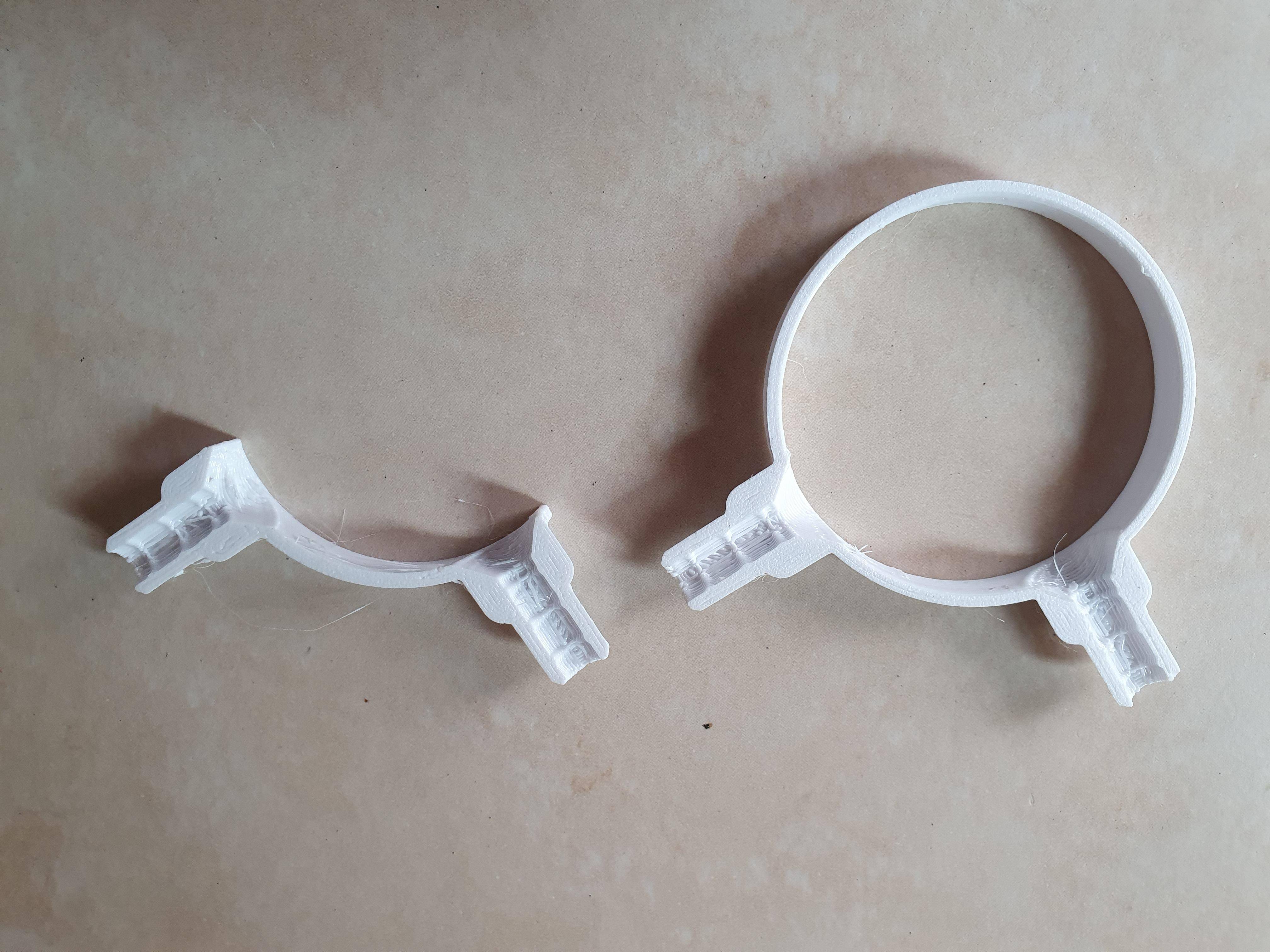
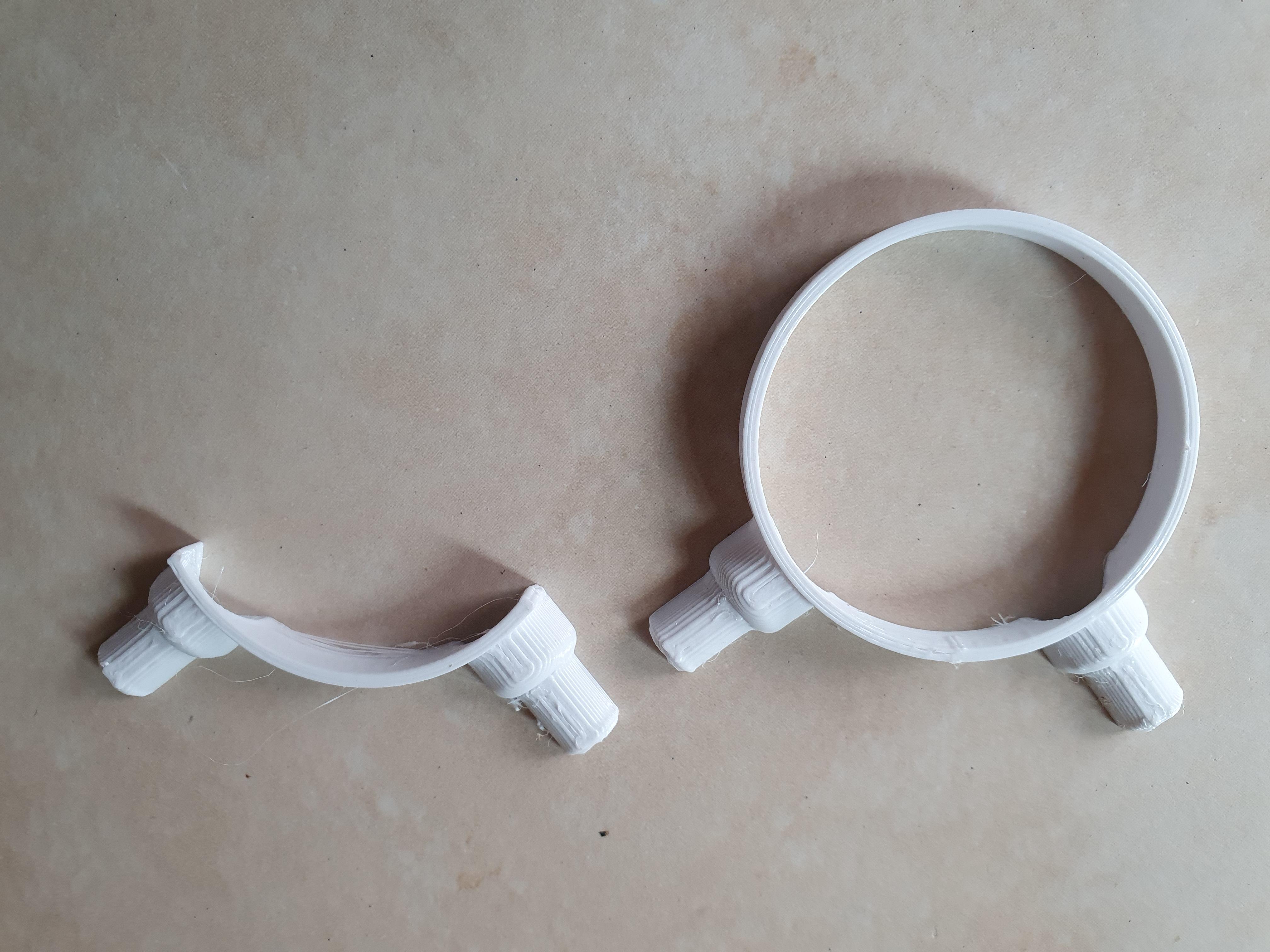
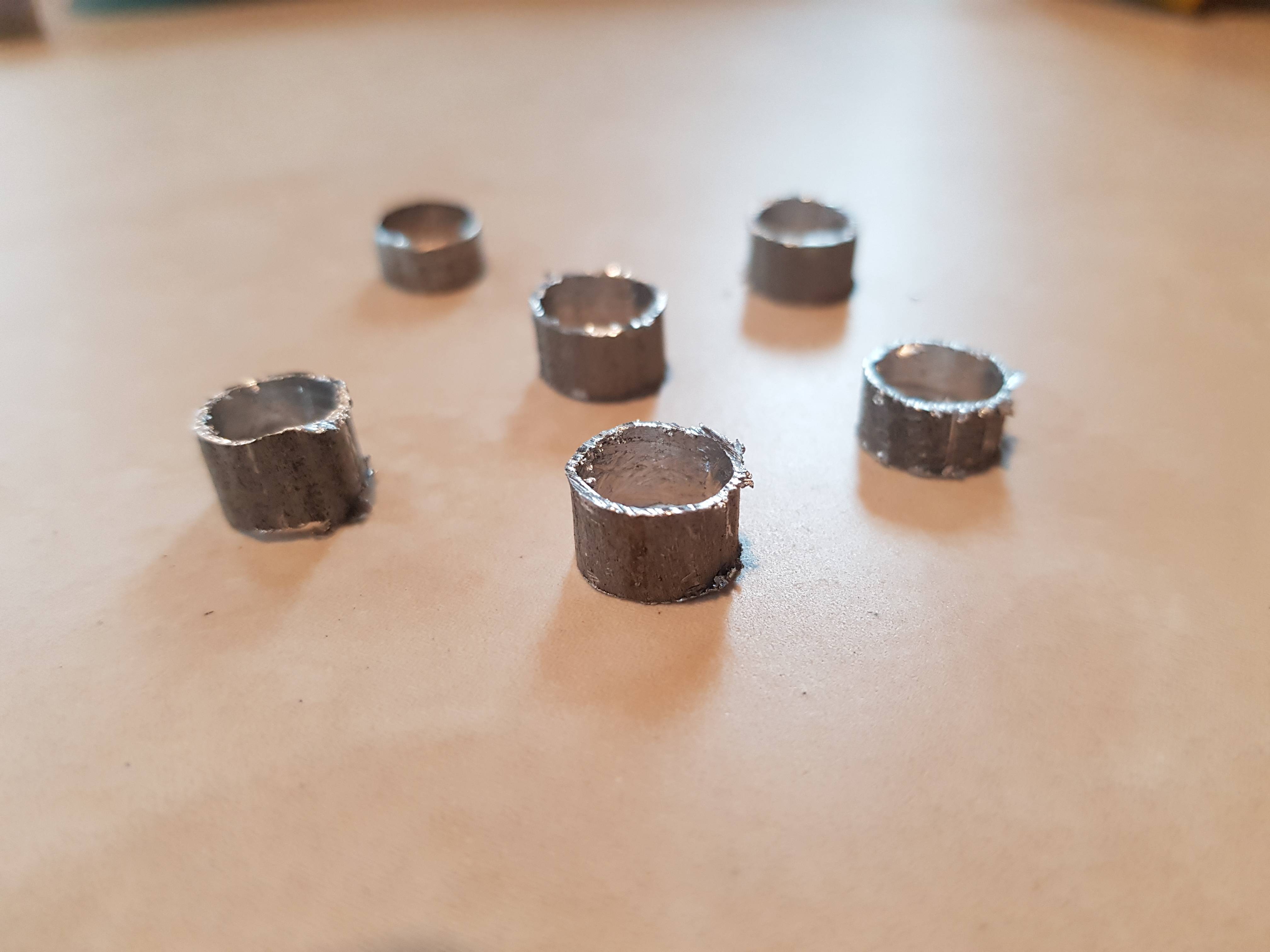
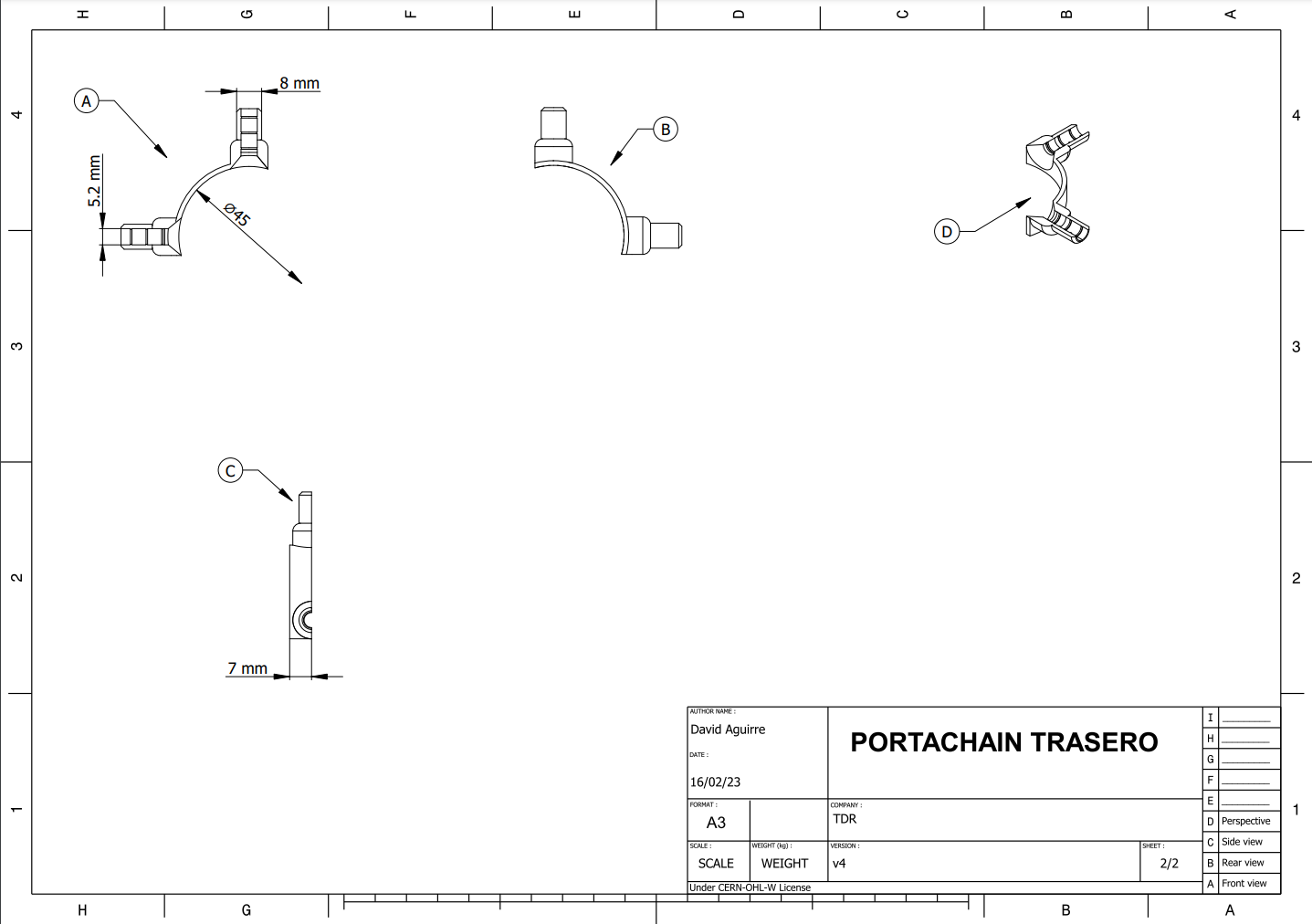
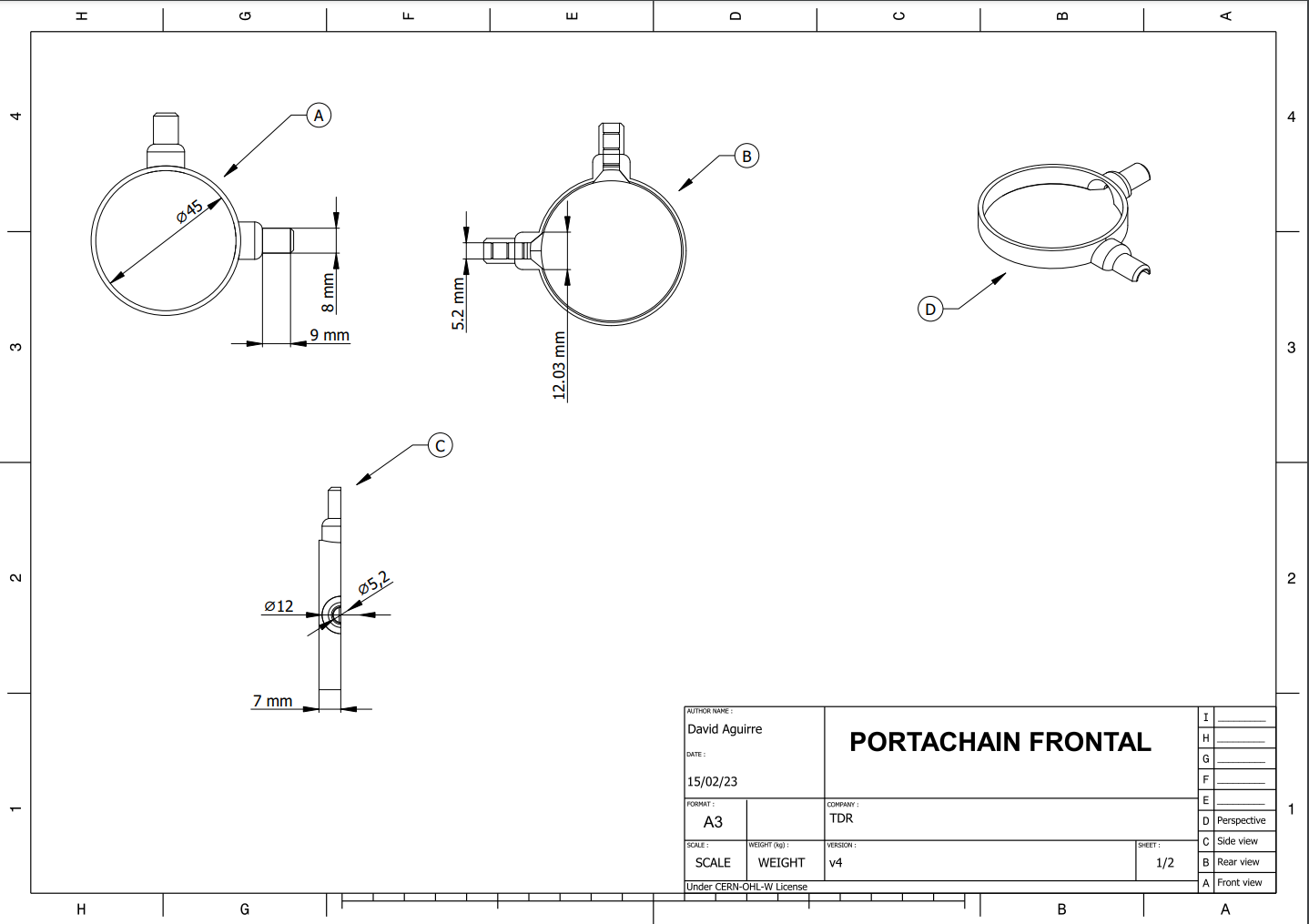
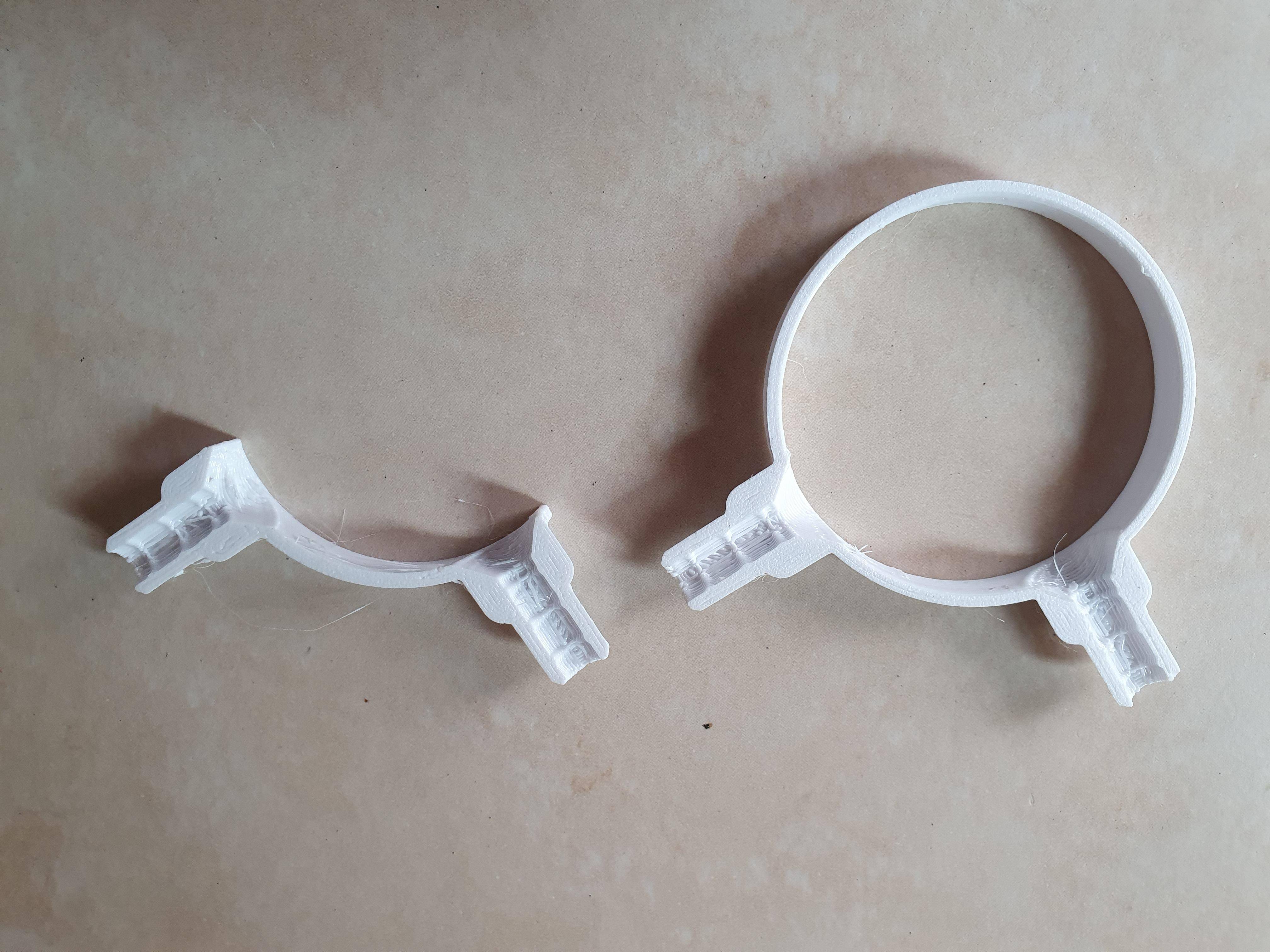
Paint
To finish the antennas, we use synthetic paint. Our first experience was to use an automotive paint over a layer of anti-rust paint. We noticed that it had the following characteristics:
- Being very resistant
- Thicker
- More value
We found it difficult to achieve the right dilution to use it, and we couldn't get a good finish. That's why we decided to try anti-rust paint which has characteristics such as:
- Converter (works on the rusted parts)
- Prevents rust
- Enamels the parts
Due to these characteristics and the ease of dilution and its covering power, we are currently using this paint as a coating for our models. For more information about the procedure, here.
Finished antenna with plastic parts
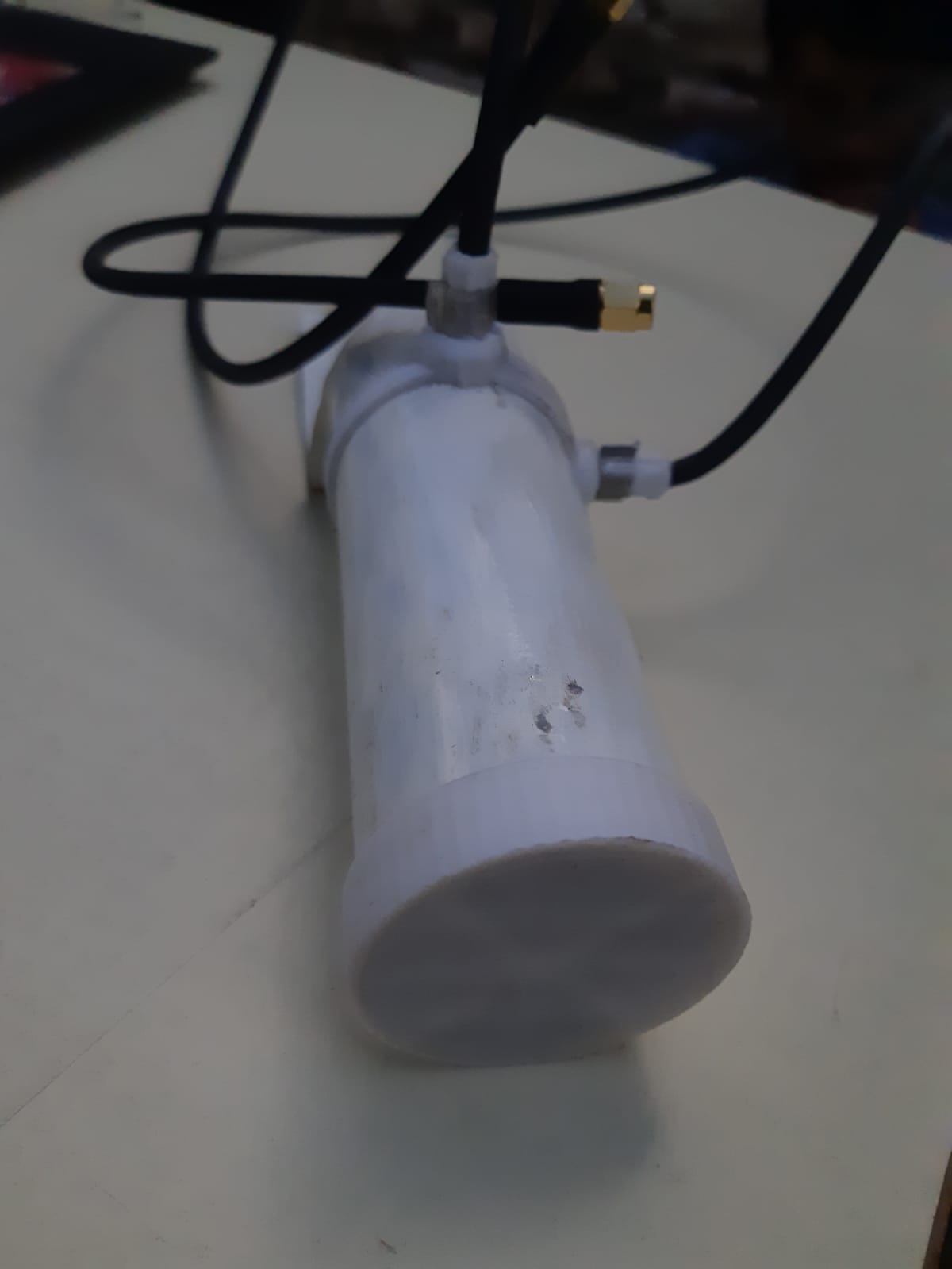
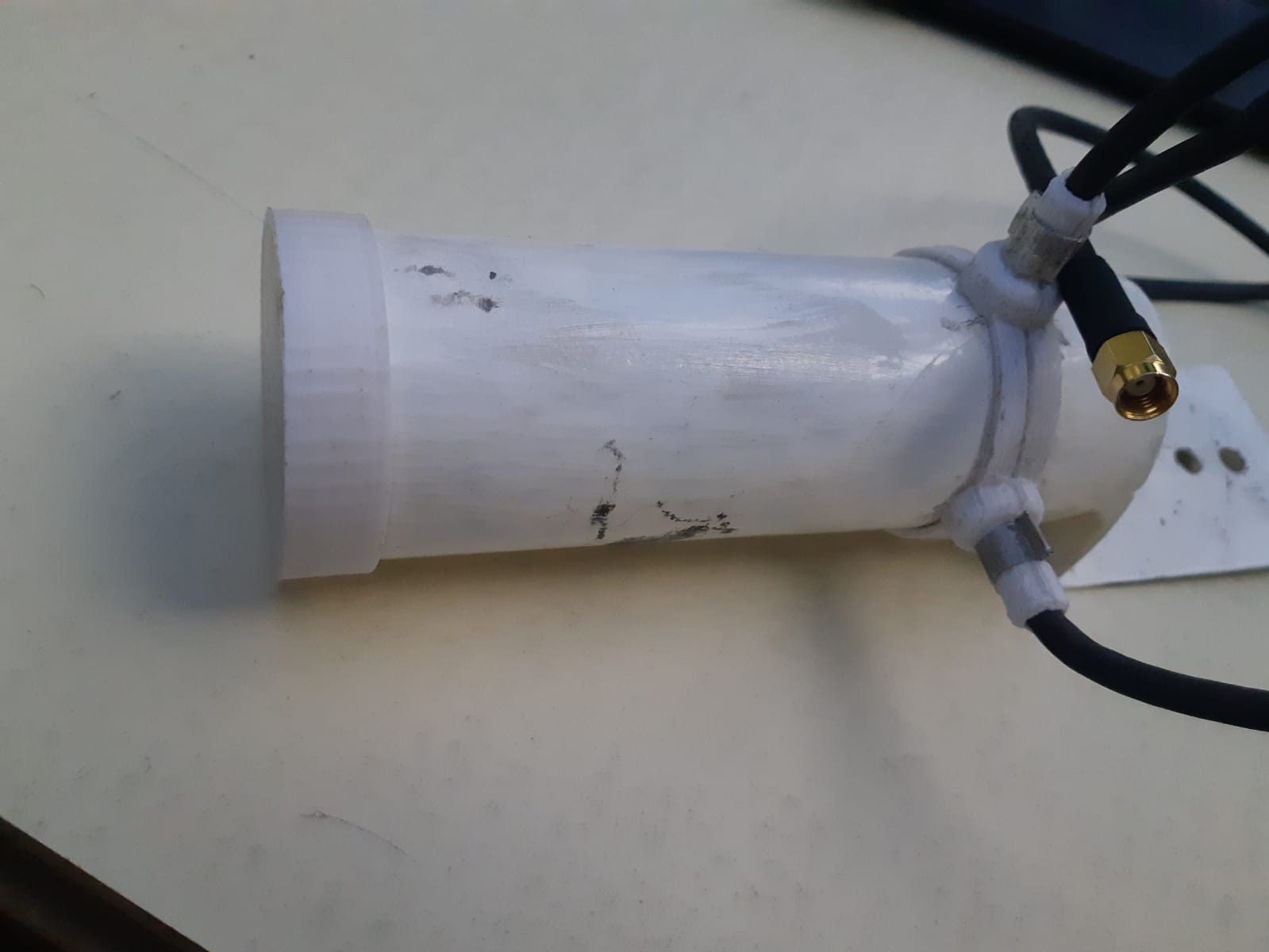
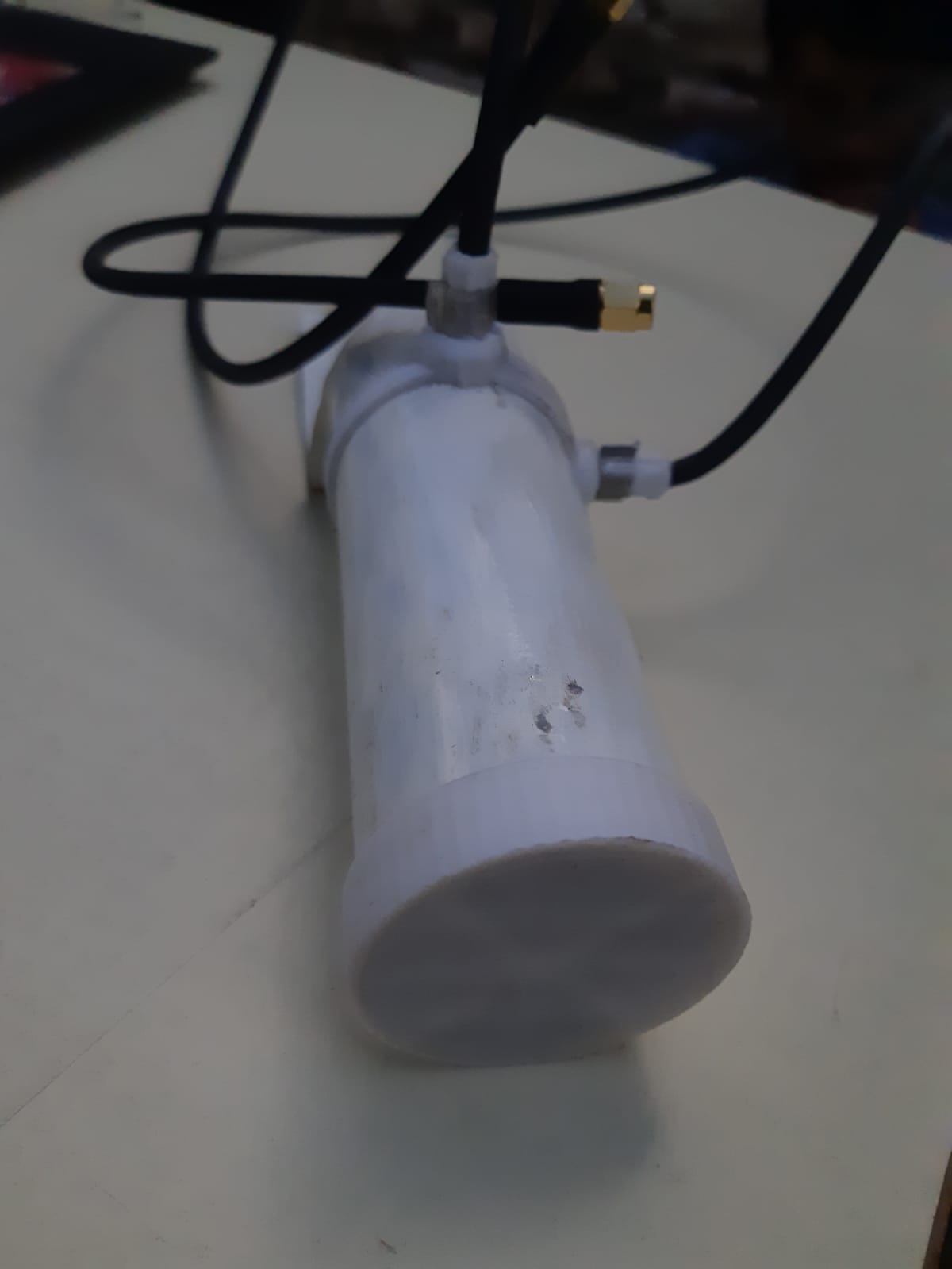
couplings for directional antenna design
We have developed several complementary parts to the waveguide, in order to increase the final directionality. The latest tests confirm that approximately 13dB of gain is achieved in one direction.
Parabola brackets allow the addition of the 16 inch secondary reflector to the waveguide. The nosepiece also covers the inside of the tube and holds the primary reflector in the focal zone of the parabola. The actual nose takes 5 hours to print, in total the necessary parts take almost 8 hours to print.
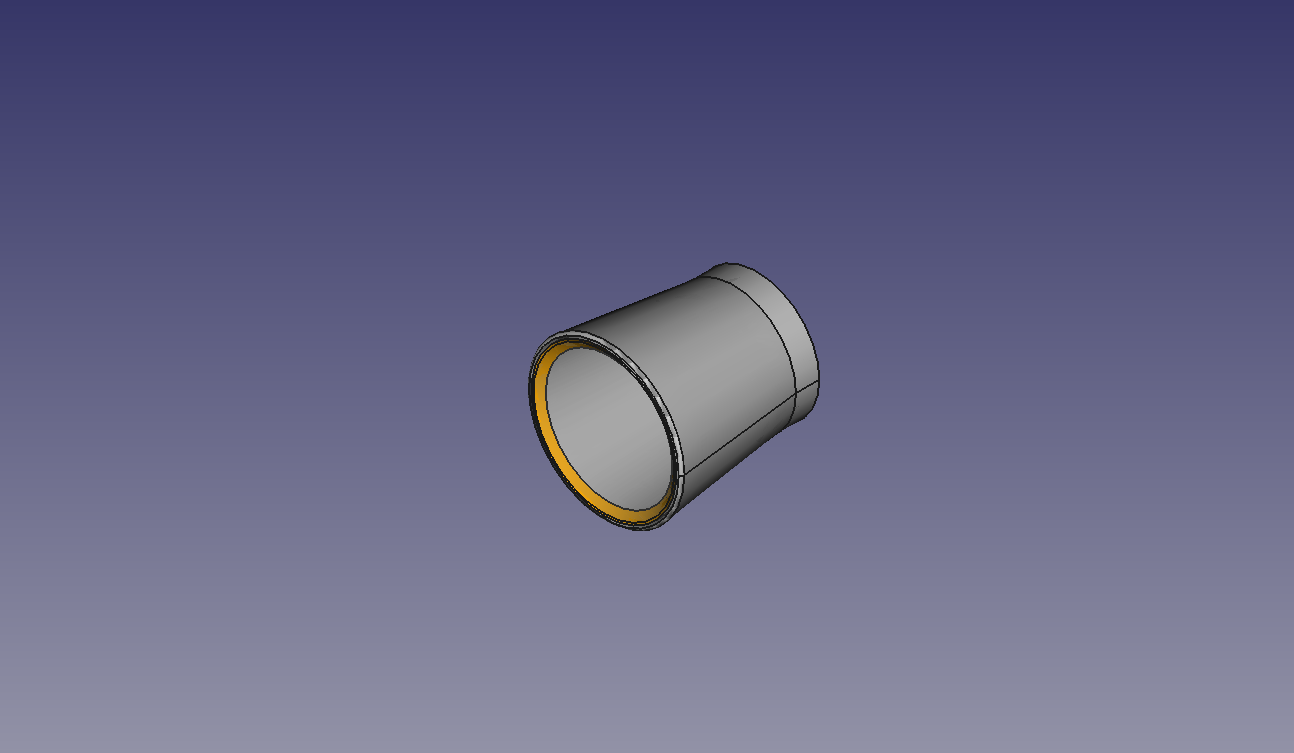
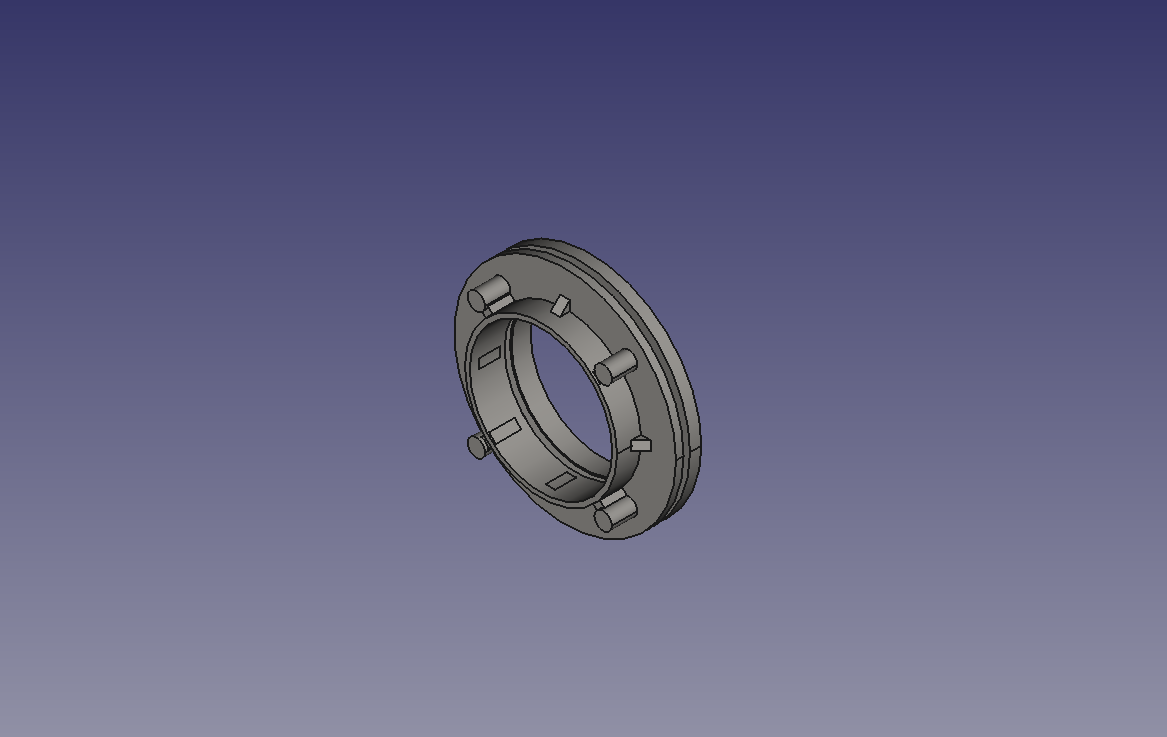
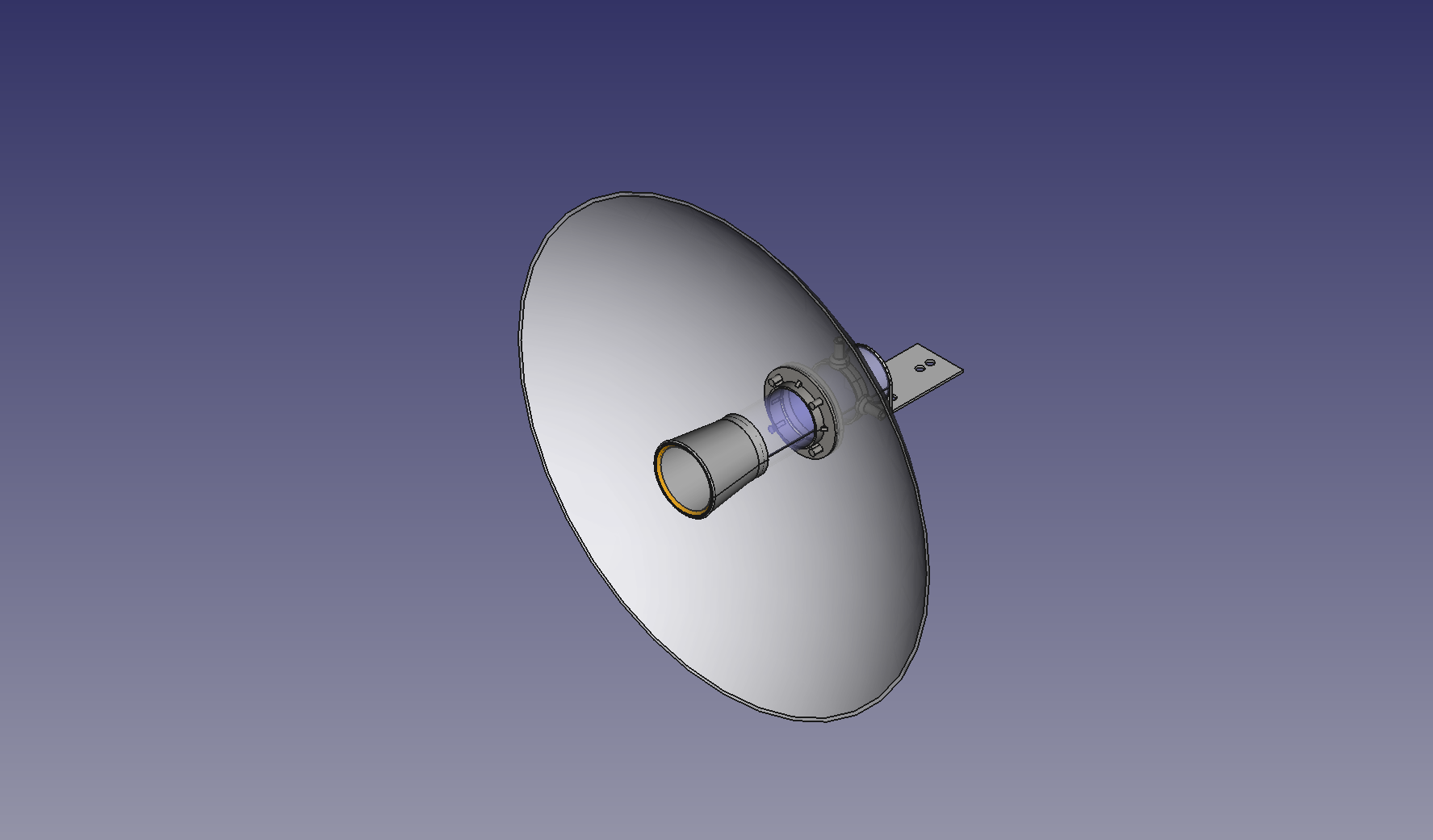
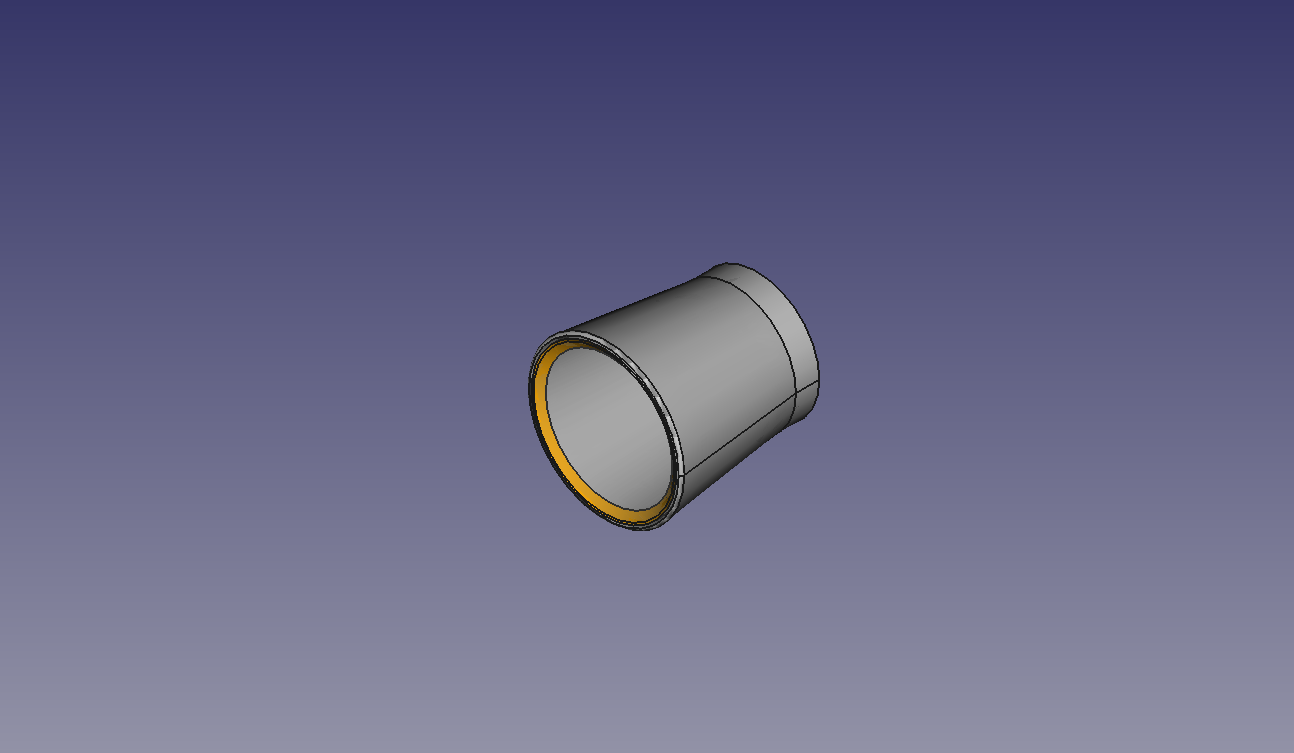
This project was funded through the User-Operated Internet fund, a fund established by NLnet made possible by financial support from the PKT Community The Network Steward and stichting Technology Commons Trust.
Saludamos a les amigues de AlterMundi.